Executive Summary

Challenge

Solution

After its initial software evaluation did not yield a solution, the automaker discovered and partnered with Sensfix because Sensfix’s AI-powered rule engine, SDM AI Workflows, had the capabilities, flexibility, and simplicity the company needed to solve its parts and consumables problem. With no coding experience required, a facility manager can now easily build any workflow through the Sensfix web app with essential information embedded in each step including the service person, spare parts and consumables required, vehicle, and tools.
Once the service is being performed, the workflow requires service personnel to swipe through the workflow steps on their mobile app and enter inventory items used. At the same time, Sensfix’s AI computer vision and natural language processing capabilities can automatically capture other specific information needed, like values from a meter or LCD display. These digitized inputs are also fed to the workflow AI engine to train the system and establish self-learning workflows.
With a fully digitized workflow and service platform in place, the automaker’s facility manager now has global visibility of all assets within the facility and every service workflow in progress. The facility manager can view detailed real-time data for assets and service including warranties, tools, vehicles, spare parts, and consumables.
To gain more control over the parts and consumables overuse, the automaker has now set limits on the usage of certain inventory items and Sensfix delivers alerts and notifications to management if any thresholds are exceeded.
Results
With Sensfix AI-powered service solutions, the automaker has improved its service efficiency by:
- Decreasing inventory overuse, theft, and loss by 80%.
- Introducing a new real-time workflow metric to track the usage of inventory.
- Enabling transparency for all stakeholders at every step of service workflows.
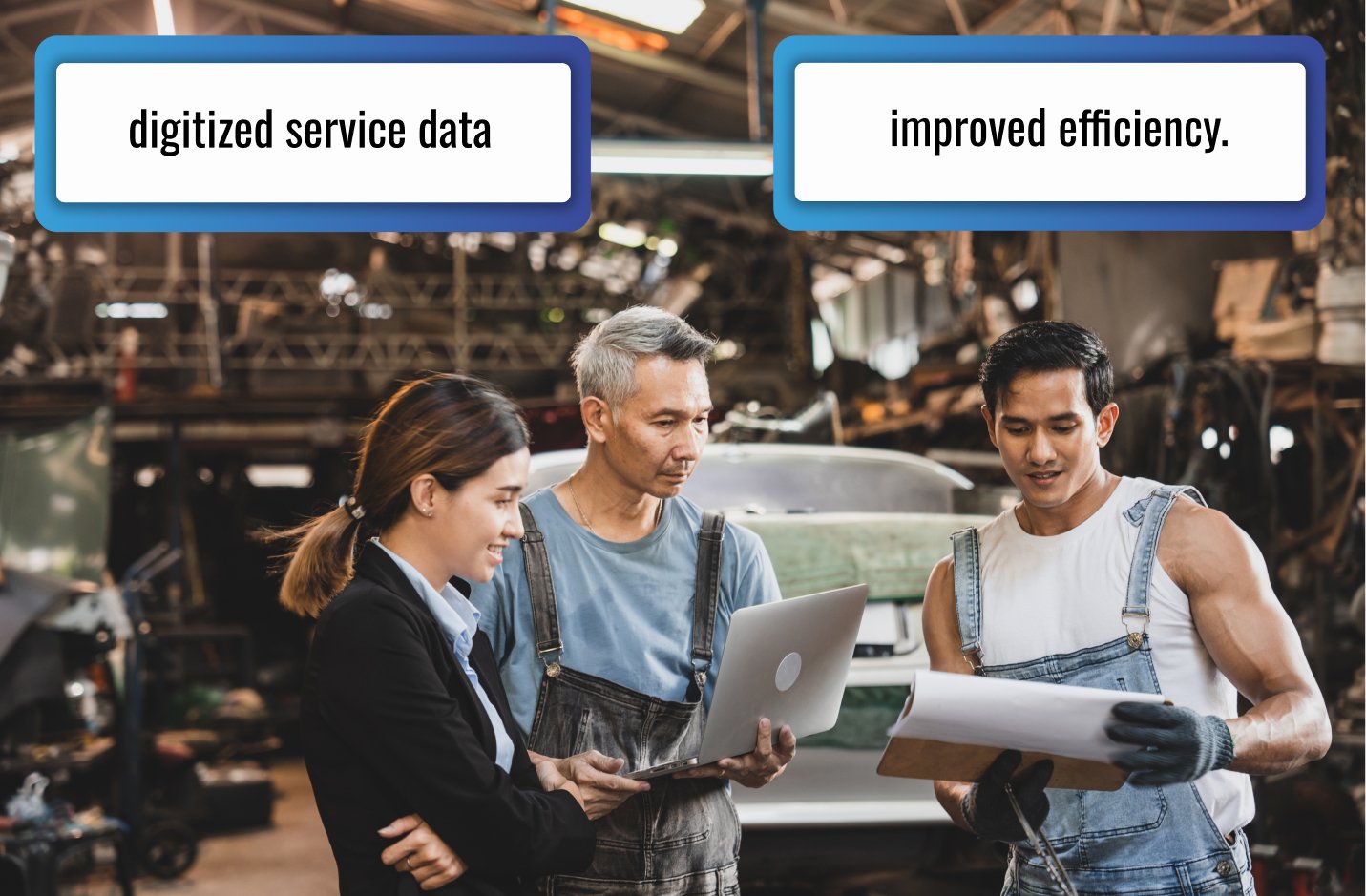
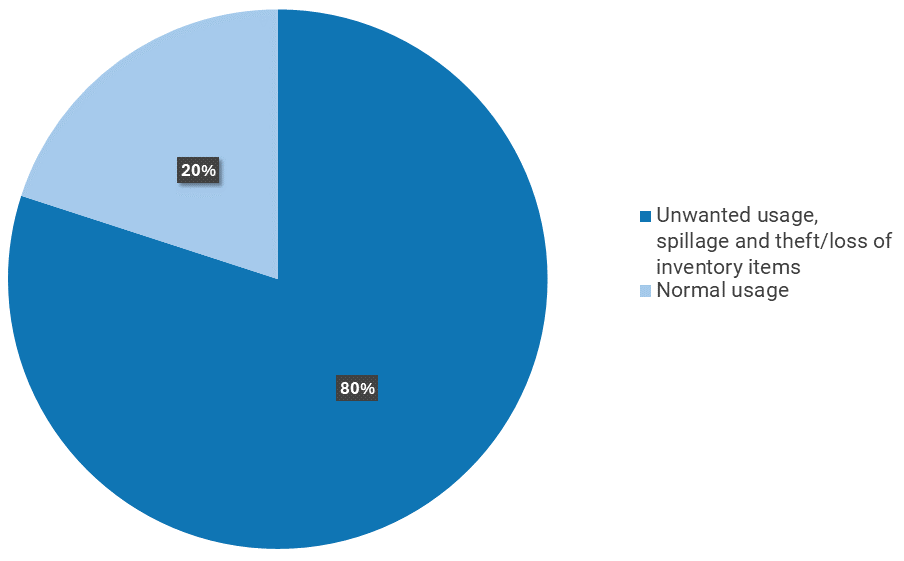